Vacuum forming is a process used to shape plastic material. It is a simplified form of thermoforming. In the vacuum forming process, a plastic sheet is heated to a high temperature, stretched on the surface of a mold, and pulled around the mold using vacuum suction. Read More…
Valk’s policy is “to meet or exceed our customer’s requirements, working together as a team with honesty and integrity.” Valk’s success is due to their long standing focus on quality & customer service.
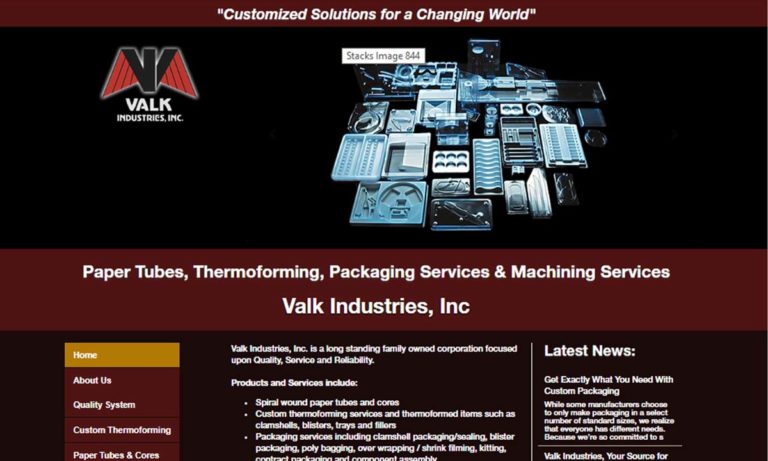
Since 1960, Profile Plastics Inc. has been at the forefront of thermoforming technology. Utilizing the latest software and technology, our expert staff of engineers can design custom vacuum, pressure, and twin-sheet thermoformed solutions. Over the last 60 years, we have developed a process that allows us to deliver consistent, high volume, and precise products with superior quality. Our high...

Quality Plastics has been a leading manufacturer of vacuum forming since 1976. Whether you need a small batch of custom vacuum-formed parts or a large-scale production run, we have the capabilities and expertise to deliver. We are committed to providing our customers with exceptional vacuum-formed products and services that meet their needs and exceed their expectations. Contact us today to learn ...

Engineered Plastic Products custom forms & fabricates sheet thermoplastic materials, standard & specialized, for any number of industrial & commercial requirements. EPP has been widely recognized for outstanding manufacturing & service since 1958 for companies such as GE, NASA & AT&T. Custom fabricated parts can be as large as 72"x108" down to 2"x2" in any thickness up to 1 1/2". Post-forming...
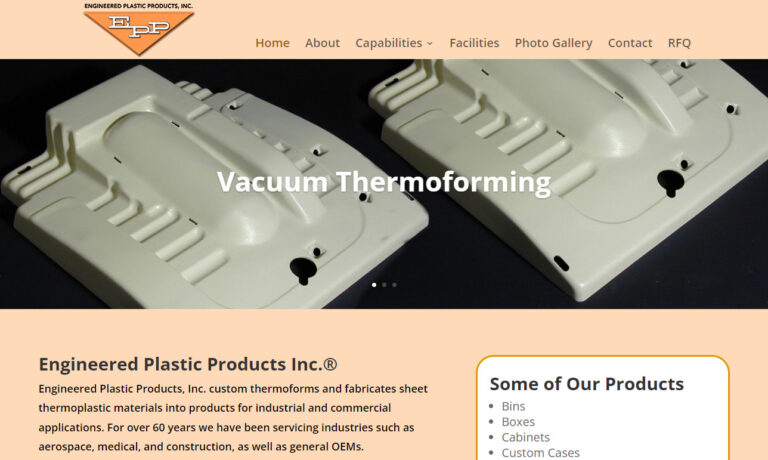
At Lerner Molded Plastics, we specialize in crafting high-quality vacuum-formed products tailored to meet the diverse needs of our clients. With years of expertise in the industry, we take pride in our ability to deliver innovative solutions that exceed expectations.

RapidMade is a leader in thermoforming and vacuum forming solutions, offering unmatched customer experience, quality, and speed. We cater to diverse needs with a broad material and equipment portfolio, ensuring cost-effective, engineered parts. Trust us for reliable, timely delivery of your small to medium batch plastic projects, meeting the highest industry standards. Choose RapidMade for...
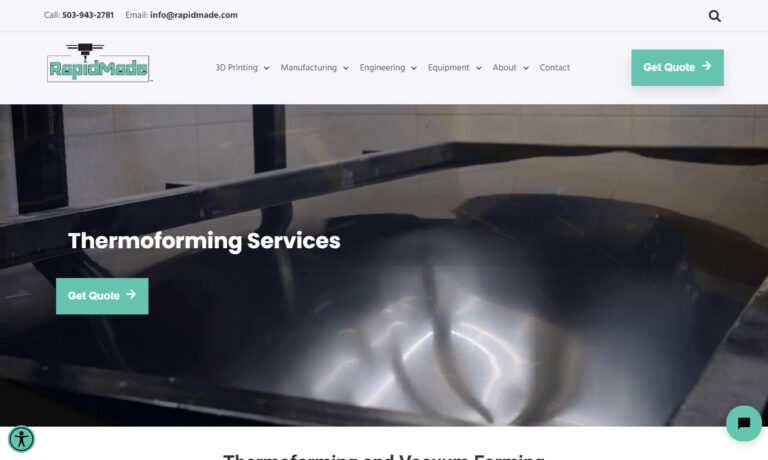
At Duo Form, we are pioneers in the realm of vacuum-formed plastic products. With a collective passion for precision engineering and creative problem-solving, we've established ourselves as leaders in delivering high-quality solutions to a wide range of industries.

Robinson Industries offers thermoformed and injection molded reusable, heavy duty plastic pallets, packaging and more. We are one of the largest suppliers of reusable pallets to many industries.
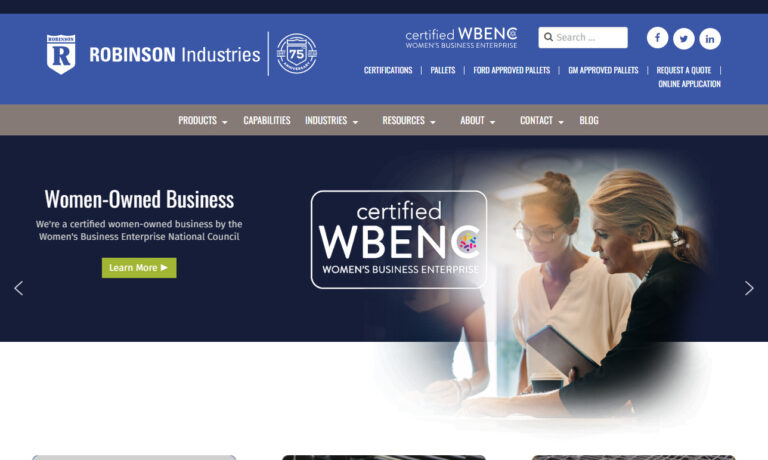
More Vacuum Formed Plastic Companies
What is Vacuum Forming
Vacuum forming is a process used to shape plastic material. It is a simplified form of thermoforming. In the vacuum forming process, a plastic sheet is heated to a high temperature, stretched on the surface of a mold, and pulled around the mold using vacuum suction. This process is used for many applications, from small parts of devices to industrial machinery. Vacuum forming is used in automobile and medical industries, consumer goods, food packaging, and packaging and display.

Process of Vacuum Forming
The steps of the vacuum forming are discussed here:
- The first step is clamping. The plastic sheet is placed in a frame and clamped into place.
- After clamping, the plastic sheet is heated to make it soft and ready for the mold.
- The heated sheet is placed over the mold and pulled across the entire surface using a vacuum.
- After the plastic is placed on the mold, the plastic is cooled. A fan or mist is applied to speed up the cooling process for large pieces.
- When the plastic has cooled, it is released from the frame.
- In some processes, excess material on the sides of the sheet will need to be trimmed.
Vacuum Formed Plastic
The plastic used for vacuum forming is called “thermoplastic.” Thermoplastic can be heated and softened repeatedly and hardened when cooled. Many different types of thermoplastics are used for this process, and each has different characteristics according to its composition. But the ideal material has high impact strength, high thermal strength, is easy to form, and has a low shrinkage level after cooling. Some of these thermoplastics are hygroscopic, meaning they must be pre-dried before being introduced into ovens.
Acrylonitrile Butadiene Styrene (ABS)
- ABS is an amorphous thermoplastic that is rigid, strong, and hygroscopic.
- Because it contains rubber, it has good weather and impact resistance.
- The shrinkage rate of this material is 0.3-0.8%.
- It is available in black, white, gray, and other limited colors.
- ABS is used in manufacturing vehicle parts, sanitary parts, electrical enclosures, and luggage.

Co-polyester (PETG)
- PETG is an amorphous thermoplastic that is easy to fabricate and optically good.
- It is safe for food applications because it can be sterilized and is resilient to acids and oils.
- It has good formability, and pre-drying is not necessary for this plastic.
- Its shrinkage rate is 0.3-0.7%.
- It is available in clear and limited colors.
- It is suitable for medical applications and display units.
Acrylic - Perspex (PMMA)
- Acrylic is an amorphous thermoplastic that performs well after forming and has good clarity.
- It is hygroscopic, brittle, and damaged by high temperatures but has medium to high strength.
- The shrinkage rate is 0.3-0.8%.
- It is available in clear or solid colors.
- It is well-suited for domes, ceilings, lights, sanitary ware, signboards, and light diffusers.

Polycarbonate (PC)
- PC is a clear, rigid, hard, and amorphous material.
- It has good clarity and is a self-extinguisher.
- Polycarbonate is very strong and hygroscopic.
- It is formidable to high definition, and the shrinkage rate is 0.6-0.8%.
- It is ideal for skylights, aircraft trims, guards, light diffusers, and signage.
Polystyrene (HIPS)
- Polystyrene is the most commonly used material; it is easy to work on and available in many patterns.
- It is not suitable outdoors because it has low UV resistance.
- It forms well with high definition, and the shrinkage rate is 0.3-0.5%.
- It is best for making disposable products, toys, models, and packaging.

Polypropylene (PP)
- It is a semi-crystalline material that is difficult to form, but its flexibility makes it ideal for many applications.
- Polypropylene is not hygroscopic and has very good strength.
- No spray works on it, and the shrinkage rate is 1.5-2.2%.
- It is used to manufacture luggage, toys, medical equipment, and chemical tanks.

Polyethylene (HDPE)
- Polyethylene is also a semi-crystalline material with good chemical resistance.
- It has good strength and is not hygroscopic.
- The shrinkage rate is 2.0-3.5%.
- It is well-suited for vehicle parts, housing, and enclosures.

Applications of Vacuum Formed Plastics
Vacuum-formed plastics are widely used in the automotive, agriculture, transport, medical, construction, housing, packaging, and renewable energy industries. Additionally, the vacuum-forming process is used to make machinery parts for vehicles. The food industry greatly relies on hygienic packaging, so vacuum forming is a frequently used process.

Choosing the Right Vacuum Formed Plastic Supplier
To make sure you have the most constructive outcome when purchasing vacuum formed plastic from a vacuum formed plastic supplier, it is important to compare several companies using our directory of vacuum formed plastic suppliers. Each vacuum formed plastic company has a business profile page that highlights their areas of experience and capabilities, along with a contact form to directly communicate with the supplier for more information or request a quote. Review each vacuum formed plastic company website using our patented website previewer to get an understanding of what each business specializes in. Then, use our simple RFQ form to contact multiple vacuum formed plastic companies with the same form.